Maximize Uptime: When to Schedule Preventive Maintenance
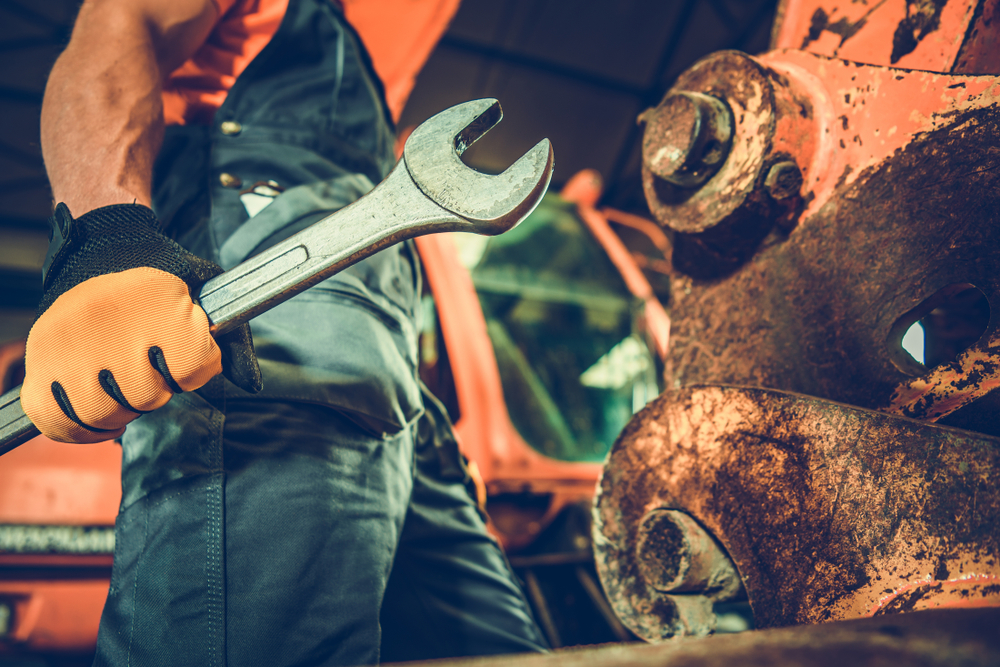
Effective preventive maintenance is the cornerstone of maximizing equipment uptime, ensuring safety, and reducing costly breakdowns. For industries that rely heavily on heavy equipment, like construction, manufacturing, and mining, creating an efficient preventive maintenance schedule can yield substantial benefits, optimizing the longevity and performance of machinery. In this guide, we’ll explore the best practices for scheduling preventive maintenance and provide tips to ensure your equipment stays operational with minimal interruptions.
Why Preventive Maintenance Matters
Preventive maintenance is a proactive approach focused on regularly scheduled maintenance tasks that aim to prevent equipment failures before they happen. Instead of waiting for breakdowns or malfunctions, preventive maintenance involves routine inspections, adjustments, cleaning, and repairs. This method is particularly beneficial for heavy equipment, where unscheduled downtime can lead to productivity losses and high repair costs.
Key Preventive Maintenance Benefits
Implementing a preventive maintenance program offers several crucial advantages:
- Reduced Downtime: By addressing potential issues before they become major problems, preventive maintenance helps prevent unexpected breakdowns, ensuring equipment is available when needed.
- Enhanced Equipment Lifespan: Regular maintenance helps keep heavy machinery in optimal condition, extending its operational life and maximizing the return on investment.
- Cost Savings: Preventive maintenance can save substantial amounts by reducing emergency repair expenses, as well as lowering energy costs by keeping equipment efficient.
- Improved Safety: Ensuring that machinery is in safe working order protects both the equipment operators and other staff on-site, reducing the risk of accidents and injuries.
- Increased Productivity: With fewer interruptions, equipment runs more smoothly, contributing to uninterrupted workflows and more reliable project timelines.
By establishing a well-thought-out preventive maintenance schedule for heavy equipment, companies can safeguard their assets and workforce while maximizing uptime.
The Basics of a Preventive Maintenance Schedule
Designing an effective preventive maintenance schedule involves considering several factors, including equipment type, usage frequency, environmental conditions, and manufacturer recommendations. Each piece of machinery has specific maintenance needs, and a one-size-fits-all approach won’t suffice. Here are the fundamental steps for creating a preventive maintenance schedule for heavy equipment:
Assess Equipment and Usage
To build a sound preventive maintenance schedule, begin with a thorough assessment of the equipment:
- Identify Essential Equipment: Determine which machines are vital to operations and prioritize them in your preventive maintenance plan.
- Analyze Usage Patterns: Track how frequently equipment is used, as well as the intensity of its operation. High-usage machinery may require more frequent maintenance than equipment used sporadically.
- Evaluate Operating Environment: Equipment used in harsh or extreme environments—such as high-dust or humid areas—may need more frequent attention than machinery used in cleaner, controlled conditions.
Develop a Preventive Maintenance Checklist
A well-crafted preventive maintenance checklist is essential for ensuring consistency in maintenance tasks. Tailor the checklist to each piece of equipment, following manufacturer guidelines and incorporating any additional tasks relevant to specific operating conditions.
Sample Preventive Maintenance Checklist for Heavy Equipment
- Inspect for leaks, loose parts, and visible wear.
- Check and refill all fluid levels, including oil, coolant, and hydraulic fluids.
- Lubricate moving parts as specified in the operator’s manual.
- Test safety devices, alarms, and controls.
- Inspect tires, tracks, or other mobility-related components for wear or damage.
- Test and inspect electrical systems and connections.
- Review maintenance logs for any unusual patterns or recurring issues.
Following a checklist ensures that no maintenance step is overlooked, helping to keep equipment in peak condition.
Determining Optimal Maintenance Intervals
Once you have established a checklist and assessed equipment needs, it’s time to decide on maintenance intervals. Finding the right timing for preventive maintenance is a balancing act: too frequent maintenance can waste resources, while insufficient maintenance may lead to breakdowns.
Factors to Consider for Scheduling Maintenance Intervals
- Manufacturer Recommendations: Most equipment manufacturers provide a preventive maintenance schedule, often based on usage hours or time intervals (e.g., every 250 operating hours or every three months). Following these recommendations is a reliable starting point.
- Usage-Based Scheduling: Many industries use “hours of operation” as a benchmark for scheduling maintenance tasks. For example, maintenance may be scheduled every 500 or 1000 hours, depending on the equipment’s demands and load.
- Calendar-Based Scheduling: Some companies prefer time-based scheduling, such as quarterly, bi-annual, or annual checks. This approach is useful when equipment usage is more predictable or when regulations require time-based inspections.
- Predictive Data: With advanced telematics, companies can monitor real-time data like vibration levels, temperature, and fuel consumption to predict maintenance needs. This data-driven approach helps fine-tune maintenance schedules, often allowing adjustments based on actual wear and tear instead of fixed intervals.
Seasonal Considerations
Certain types of equipment experience seasonal variations in usage, particularly in construction and agricultural sectors. Adjusting preventive maintenance schedules to align with peak and off-peak seasons can optimize uptime. For example, scheduling maintenance during winter for equipment primarily used in summer ensures it’s ready for high demand.
Leveraging Technology for Efficient Maintenance
The advent of digital tools has transformed the preventive maintenance process. Computerized Maintenance Management Systems (CMMS) and telematics make it easier to track equipment performance, monitor usage, and schedule maintenance based on real-time data.
Advantages of Using a CMMS
A CMMS can streamline your preventive maintenance program in several ways:
- Automated Scheduling: CMMS allows you to automate maintenance schedules, minimizing the risk of human error in tracking maintenance intervals.
- Comprehensive Documentation: Maintenance logs, inspection results, and repair histories are centralized, ensuring easy access to past records.
- Inventory Management: CMMS tracks inventory levels of spare parts, helping prevent delays caused by part shortages.
- Data Analytics: Detailed reporting tools offer insights into equipment health, helping refine the preventive maintenance schedule over time.
With these advantages, CMMS can significantly enhance a preventive maintenance program’s effectiveness, reducing downtime and extending equipment life.
Monitoring and Adjusting the Schedule
A preventive maintenance schedule is not a “set it and forget it” document. Regular reviews of equipment performance and maintenance logs are necessary to ensure the schedule remains effective. Adjust the schedule as needed based on actual maintenance data.
Key Performance Indicators (KPIs) for Maintenance
Monitoring KPIs can offer valuable insights into how well your preventive maintenance program is functioning:
- Mean Time Between Failures (MTBF): Measures average uptime between repairs, indicating equipment reliability.
- Mean Time to Repair (MTTR): Calculates the average time taken to complete repairs, showing maintenance efficiency.
- Maintenance Cost per Hour of Operation: Helps track overall maintenance expenses relative to usage, useful for budgeting and cost control.
- Equipment Downtime: The total time equipment is out of operation, reflecting the program’s impact on uptime.
Using these metrics, companies can continually improve their preventive maintenance approach, refining schedules based on the real-world performance of equipment.
Best Times for Scheduling Preventive Maintenance
Strategically planning maintenance during specific times can further enhance equipment availability and reduce disruption to operations.
Off-Peak Hours or Non-Working Days
Scheduling maintenance outside of peak production hours, such as during evenings, weekends, or company holidays, minimizes operational interruptions. This approach is particularly effective for machinery that is critical to round-the-clock operations.
Seasonal Downtime
If your business is seasonal, aim to perform intensive maintenance during off-season periods. Agricultural and construction sectors, for instance, often perform preventive maintenance during winter to ensure machinery is ready for peak spring and summer usage.
Scheduled Project Breaks
For industries working on project-based schedules, timing maintenance during planned breaks in activity can help avoid unscheduled interruptions. Construction projects often have planned downtimes between phases, providing an ideal opportunity for equipment maintenance.
Creating a Sustainable Preventive Maintenance Culture
Building a preventive maintenance culture within the company is vital for sustaining the program’s long-term benefits. Employees, particularly operators, play an important role in reporting early signs of issues, conducting basic maintenance, and adhering to the preventive maintenance schedule.
Training and Empowerment
- Operator Training: Train operators on the basics of equipment maintenance, including daily checks and proper usage techniques.
- Clear Communication: Ensure that maintenance schedules are well-communicated to all team members, and that everyone understands their role in maintaining equipment health.
- Incentivize Reporting: Encourage operators to report issues immediately. Incentives can be offered for timely reports that prevent larger, more costly problems.
Regular Reviews and Feedback
Hold periodic reviews of the preventive maintenance program to assess effectiveness. Include feedback from operators, mechanics, and managers to identify areas for improvement and refine the maintenance schedule as needed.
Conclusion
A well-implemented preventive maintenance schedule is the key to maximizing uptime, enhancing safety, and optimizing costs for heavy equipment. By assessing equipment needs, developing a thorough checklist, leveraging technology, and strategically timing maintenance, companies can ensure that their equipment remains in optimal condition, reducing the risk of costly breakdowns. Remember, preventive maintenance is an ongoing commitment; regular reviews and adjustments to the schedule ensure that it continues to meet operational needs efficiently.