The Role of Regular Inspections in Preventing Costly Heavy Equipment Breakdowns
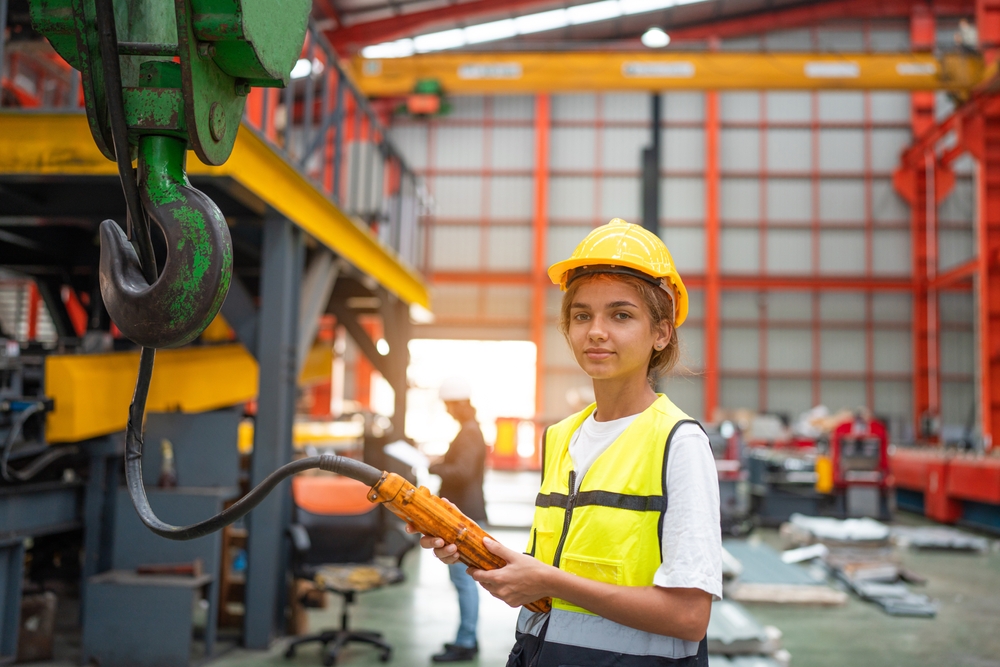
When managing a fleet of heavy equipment in places like Oregon, it is essential to prioritize consistent equipment maintenance and inspections to ensure machinery operates at peak performance. Heavy equipment, from bulldozers and excavators to cranes and loaders, forms the backbone of numerous industries, including construction, mining, and agriculture. With their high initial investment and critical role in daily operations, the cost of an unexpected breakdown can be staggering. Regular inspections play a vital role in preventing costly heavy equipment breakdowns by identifying potential issues early on, ultimately saving money and reducing downtime. In this blog post, we will explore the importance of regular inspections, how they contribute to preventing breakdowns, and why a solid maintenance strategy is essential for businesses in Oregon, including places like Lexington, OR.
The Importance of Daily Equipment Inspections
Heavy equipment inspection is an integral part of any successful fleet management strategy, particularly when operating in demanding environments such as Oregon. The nature of heavy machinery means that small problems can quickly escalate into significant failures if not detected and addressed in a timely manner. While preventive maintenance is vital, daily equipment inspections act as the first line of defense against unforeseen issues. These inspections allow operators to identify and address potential problems before they become costly repairs.
In Oregon, where environmental conditions can vary greatly, daily inspections become even more critical. The state’s frequent rain, fluctuating temperatures, and diverse terrain can accelerate wear and tear on equipment, making it essential for operators to check key components such as hydraulic systems, engine conditions, and tire pressure. By focusing on daily inspections, fleet managers can ensure that all equipment is operating safely and efficiently, helping prevent costly breakdowns that may otherwise be avoided.
How Regular Inspections Prevent Breakdowns
Preventing breakdowns is not just about repairing existing issues—it’s about identifying and addressing potential problems before they disrupt operations. Regular heavy equipment inspections are crucial for detecting issues that might not be immediately visible during normal use. Through detailed inspections, technicians can identify worn-out parts, leaking fluids, misaligned components, or faulty electrical systems that could lead to malfunctions if left unchecked.
In Oregon, where unpredictable weather conditions and rough terrain are common, regular inspections become even more critical. Rain, snow, and mud can accelerate the deterioration of equipment, especially in areas like Lexington, OR, where heavy machinery is often used in rugged environments. By performing regular inspections, operators and fleet managers can catch problems early, such as cracks in hydraulic hoses or signs of excessive rust on metal surfaces, which could potentially lead to a breakdown if ignored. Addressing these issues proactively can prevent significant damage and extend the lifespan of the equipment, ultimately reducing the overall cost of ownership.
Establishing a Comprehensive Heavy Equipment Inspection Checklist
A thorough heavy equipment inspection checklist is an invaluable tool for maintaining the longevity of your fleet and preventing unnecessary breakdowns. The checklist should cover every critical aspect of the equipment, including but not limited to engine components, hydraulic systems, tires, and electrical systems. In Oregon, where the environmental factors can place additional stress on machinery, it is essential that inspections are comprehensive and tailored to address specific regional concerns, such as corrosion from exposure to rain or debris buildup from working on rough terrain.
For instance, operators in areas like Lexington, OR, where dust and dirt are prevalent, should focus on checking air filters, fuel filters, and cooling systems regularly. Additionally, parts that are more likely to wear down quickly, such as belts, hoses, and tires, should be scrutinized during each inspection. Establishing a well-documented checklist that is consistently followed helps ensure that no part of the equipment is overlooked and provides a baseline for maintenance schedules and tracking performance.
The Role of Fleet Maintenance in Preventing Costly Breakdowns
A well-structured fleet maintenance program plays a pivotal role in preventing costly heavy equipment breakdowns, especially in industries that rely heavily on machinery in areas like Oregon. Regular inspections are just one piece of the puzzle—effective fleet maintenance involves creating a schedule that outlines routine tasks, such as oil changes, fluid checks, and part replacements, in addition to regular inspections. When fleet maintenance is done consistently and thoroughly, the likelihood of encountering costly and disruptive breakdowns decreases significantly.
In Oregon, fleet maintenance is crucial to protect against external factors that might accelerate equipment wear. For example, equipment used in logging or construction projects in rugged regions like Lexington, OR, might be subject to extreme pressure from both physical stress and environmental elements. A solid fleet maintenance program ensures that necessary repairs are made in advance, and components are replaced as needed before they have a chance to fail. This proactive approach can prevent issues that would otherwise lead to unscheduled downtime and expensive repairs.
Moreover, keeping detailed records of inspections and maintenance work allows fleet managers to track the health of each piece of equipment. This data can help identify trends, such as recurring issues with specific parts or machines, which can inform future purchasing or maintenance decisions.
Long-Term Benefits of Regular Inspections for Oregon Businesses
For businesses in Oregon, the role of regular heavy equipment inspections cannot be overstated. Regular inspections not only help prevent costly breakdowns but also contribute to the long-term success of operations by improving safety, efficiency, and compliance with regulations. In a state where many industries rely on heavy equipment for day-to-day operations, ensuring that all machinery is in optimal condition is key to maintaining productivity and meeting project deadlines.
In addition to preventing breakdowns, regular inspections can also lead to cost savings in terms of fuel efficiency. Well-maintained equipment tends to perform more efficiently, using less fuel and reducing operational costs. Moreover, by extending the lifespan of heavy machinery, businesses can avoid the hefty capital costs associated with purchasing new equipment prematurely.
Furthermore, keeping equipment in top condition helps maintain a positive reputation for businesses. In industries like construction, where equipment downtime can directly impact project timelines, ensuring that heavy equipment is operational and reliable can improve customer satisfaction and the ability to win future contracts.
Conclusion
The role of regular inspections in preventing costly heavy equipment breakdowns is clear. For businesses in Oregon, including those in areas like Lexington, OR, the benefits of regular inspections far outweigh the risks of neglecting equipment maintenance. Not only do these inspections help identify issues before they escalate, but they also contribute to improved efficiency, safety, and cost savings. By establishing a comprehensive inspection checklist, investing in fleet maintenance, and prioritizing daily equipment checks, businesses can protect their investments, minimize costly repairs, and keep their operations running smoothly.