How to Troubleshoot Electrical Problems in Heavy Equipment
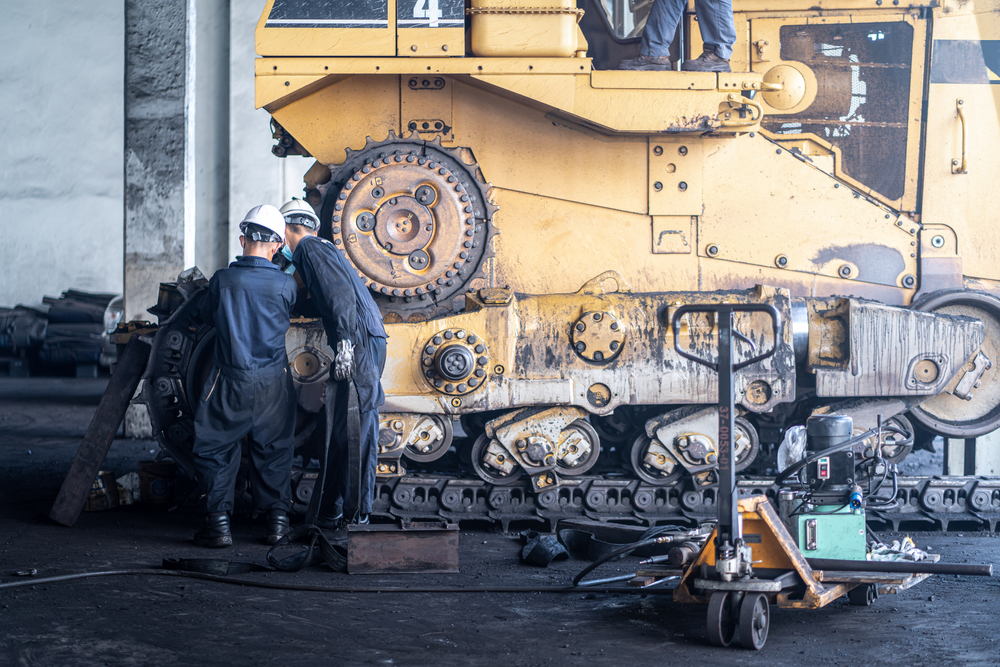
Heavy equipment plays a crucial role in various industries, from construction to agriculture. However, like any machinery, electrical issues can arise unexpectedly, causing downtime and delays. Knowing how to diagnose and troubleshoot these electrical problems is essential for minimizing disruptions and maintaining productivity. In this comprehensive guide, we will explore effective strategies and methods for troubleshooting electrical problems in heavy equipment.
Understanding Common Electrical Issues in Heavy Equipment
Before diving into troubleshooting techniques, it’s important to understand the typical electrical problems that can affect heavy machinery. These may include:
1. Battery Issues
Batteries are fundamental to the electrical system of heavy equipment. Common issues include:
- Dead Batteries: Failure to start due to insufficient charge.
- Corrosion: Build-up on terminals affecting conductivity.
- Battery Drain: Parasitic draw causing slow discharge.
2. Wiring and Connection Problems
The wiring harness and connections are susceptible to:
- Corrosion: Moisture leading to rust and poor connections.
- Chafing: Wear and tear causing exposed wires and short circuits.
- Loose Connections: Intermittent faults due to poor contact.
3. Charging System Malfunctions
The alternator and voltage regulator can experience:
- Failed Components: Such as diodes or voltage regulators.
- Belt Issues: Loose or broken belts affecting alternator performance.
- Voltage Irregularities: Overcharging or undercharging the battery.
4. Starter Motor Failures
Issues with the starter motor can manifest as:
- Clicking Sounds: Insufficient power reaching the starter.
- Failed Solenoid: Inability to engage the starter motor.
- Overheating: Due to prolonged cranking without starting.
5. Electrical Component Failures
Various components like relays, fuses, and switches may:
- Blow Fuses: Overloads or short circuits.
- Stuck Relays: Preventing proper circuit operation.
- Switch Failures: Inability to activate or deactivate systems.
Steps to Diagnose Electrical Faults
Now that we’ve identified potential issues, let’s outline a systematic approach to diagnose and troubleshoot electrical faults in heavy equipment.
Step 1: Gather Information and Symptoms
Before starting any diagnostics:
- Interview Operators: Obtain details of any observed symptoms or changes in equipment behavior.
- Check Service Records: Review maintenance logs for recent repairs or issues.
- Inspect Visual Clues: Look for visible signs of damage, corrosion, or abnormalities.
Step 2: Perform Initial Checks
Begin with basic checks to rule out simple problems:
- Battery Voltage: Measure battery voltage using a multimeter.
- Visual Inspection: Look for loose connections, corrosion, or damaged wires.
- Check Fuses and Relays: Inspect for blown fuses or faulty relays.
Step 3: Use Diagnostic Tools
Utilize diagnostic tools and equipment for accurate assessments:
- Multimeter: Measure voltage, continuity, and resistance.
- Circuit Tester: Check for power and ground at various points.
- Scan Tool (If Applicable): Retrieve error codes and data from onboard diagnostic systems.
Step 4: Test Components and Circuits
Systematically test individual components and circuits:
- Starter Motor: Test for power at the solenoid and motor terminals.
- Charging System: Measure voltage output from the alternator.
- Switches and Sensors: Verify operation and continuity.
Step 5: Narrow Down the Issue
Based on findings from tests:
- Isolate Faulty Components: Replace or repair identified faulty components.
- Address Wiring Problems: Repair damaged or corroded wires and connectors.
- Verify Repairs: Ensure repairs have resolved the issue before reassembly.
Step 6: Document and Follow Up
Document all findings and repairs:
- Create a Maintenance Log: Record diagnostics performed and parts replaced.
- Schedule Follow-Up Checks: Ensure continued reliability and prevent recurrence.
Conclusion
Troubleshooting electrical problems in heavy equipment requires a methodical approach and the right tools. By understanding common issues, performing systematic diagnostics, and addressing problems promptly, you can minimize downtime and keep your heavy machinery operating efficiently. Remember, regular maintenance and proactive inspections are key to preventing electrical faults and ensuring reliable performance.
Need Heavy Equipment Services in Lexington, OR?
Bailey Heavy Equipment Repair, Inc. is a family-owned and -operated heavy-duty equipment repair service based in Lexington, Oregon since 1984. We specialize in providing for all of your equipment repair needs, whether it’s farm equipment, utility equipment, trucks, cylinders, or something else entirely. We offer ANSI Inspections and Dielectric testing, field repair and on-site repair, line boring services, welding, machining, hose assemblies, steel sales, and other machine products. Give us a call today for more information!