Common Hydraulic Problems in Heavy Equipment and Their Solutions
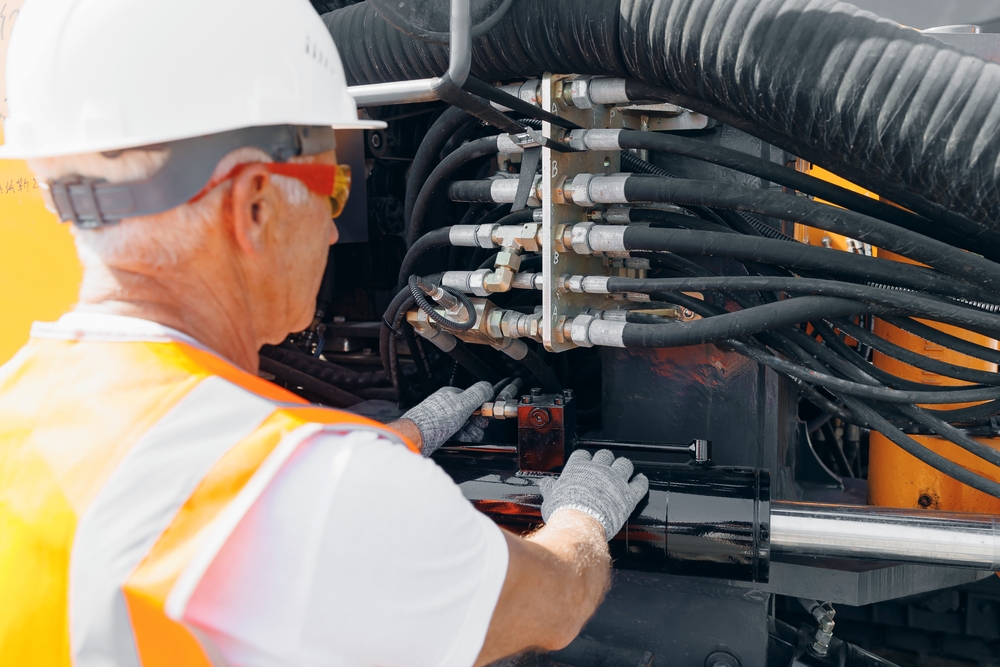
Hydraulic systems are vital components in heavy equipment, enabling them to perform heavy-duty tasks efficiently. However, like any complex machinery, hydraulic systems in heavy equipment are prone to various issues that can disrupt operations and lead to downtime. Understanding these common hydraulic problems and their solutions is crucial for maintaining equipment reliability and productivity.
Hydraulic Systems in Heavy Equipment
Heavy equipment relies on hydraulic systems for powering numerous functions such as lifting, steering, braking, and more. These systems use pressurized fluid to transmit power, making them highly efficient and capable of handling substantial loads. Despite their robust design, hydraulic systems can encounter several issues over time due to wear, contamination, or improper maintenance.
Importance of Regular Maintenance
Proper maintenance is key to preventing hydraulic failures in heavy equipment. Regular inspections, fluid checks, and servicing help identify potential issues early, ensuring optimal performance and extending the lifespan of hydraulic components.
Common Hydraulic Problems in Heavy Equipment
1. Fluid Contamination
Contaminants such as dirt, debris, water, and air can enter the hydraulic fluid, leading to accelerated wear and tear on system components. Common sources of contamination include poor sealing, dirty work environments, and improper fluid handling.
Solution: Regularly check and replace hydraulic fluid as recommended by the equipment manufacturer. Use high-quality filters and ensure seals are intact to prevent contaminants from entering the system.
2. Leaks
Hydraulic leaks can occur at hose connections, fittings, seals, or hydraulic cylinders. These leaks not only lead to fluid loss but also compromise system pressure and efficiency. Common signs include visible puddles of fluid under the equipment or decreased hydraulic performance.
Solution: Inspect hydraulic lines, hoses, and connections for leaks regularly. Replace damaged seals or hoses promptly to prevent further fluid loss and maintain optimal hydraulic pressure.
3. Cavitation
Cavitation occurs when air bubbles form and collapse within the hydraulic fluid due to low pressure. This phenomenon can cause damage to pump components and decrease hydraulic system efficiency. It often manifests as a buzzing or rattling noise during equipment operation.
Solution: Ensure hydraulic fluid levels are adequate and that intake lines are free from restrictions. Address any air leaks in the suction line promptly to prevent cavitation and maintain smooth system operation.
4. Overheating
Excessive heat can degrade hydraulic fluid and damage seals and hoses within the system. Overheating is typically caused by high ambient temperatures, overloading the equipment, or continuous operation without adequate cooling.
Solution: Monitor hydraulic fluid temperature regularly using gauges or sensors. Ensure cooling systems such as fans, radiators, or oil coolers are clean and functioning properly. Use high-quality hydraulic fluid with the appropriate viscosity for the operating conditions.
5. Component Wear and Tear
Heavy equipment undergoes significant stress during operation, leading to wear on hydraulic components such as pumps, valves, and cylinders. Over time, this wear can cause reduced performance, increased friction, and eventual component failure.
Solution: Implement a preventive maintenance schedule that includes inspections and component replacements based on manufacturer recommendations. Regularly check for signs of wear such as fluid leaks, unusual noises, or decreased hydraulic efficiency.
6. Air Ingress
Air can enter the hydraulic system during fluid replacement, component repairs, or due to faulty seals and fittings. The presence of air can lead to reduced system efficiency, erratic operation, and potential damage to hydraulic components.
Solution: Bleed air from the system using recommended procedures after any maintenance or repair work. Inspect seals and fittings regularly and replace damaged components to prevent air ingress into the hydraulic system.
Conclusion
Maintaining optimal hydraulic system performance in heavy equipment requires proactive maintenance, regular inspections, and prompt resolution of identified issues. By understanding the common hydraulic problems outlined above and implementing effective solutions, equipment operators and maintenance personnel can minimize downtime, reduce repair costs, and extend the operational lifespan of their heavy equipment.
Need Heavy Equipment Services in Lexington, OR?
Bailey Heavy Equipment Repair, Inc. is a family-owned and -operated heavy-duty equipment repair service based in Lexington, Oregon since 1984. We specialize in providing for all of your equipment repair needs, whether it’s farm equipment, utility equipment, trucks, cylinders, or something else entirely. We offer ANSI Inspections and Dielectric testing, field repair and on-site repair, line boring services, welding, machining, hose assemblies, steel sales, and other machine products. Give us a call today for more information!